1. පළමු පියවර: උණු කිරීම
ඇලුමිනියම් කාර්මික පරිමාණයෙන් විද්යුත් විච්ඡේදනය භාවිතයෙන් නිපදවන අතර ඇලුමිනියම් උණු කරන්නන්ට කාර්යක්ෂමව ක්රියාත්මක වීමට විශාල ශක්තියක් අවශ්ය වේ. බලශක්තිය සඳහා ඒවායේ අවශ්යතාවය නිසා උණු කරන්නන් බොහෝ විට ප්රධාන බලාගාරවලට යාබදව පිහිටා ඇත. බල පිරිවැයේ ඕනෑම වැඩිවීමක් හෝ ඇලුමිනියම් ඉහළ ශ්රේණියකට පිරිපහදු කිරීමට අවශ්ය බල ප්රමාණය ඇලුමිනියම් දඟරවල පිරිවැය වැඩි කරයි. ඊට අමතරව, විසුරුවා හරින ලද ඇලුමිනියම් වෙන් වී එකතු කිරීමේ ප්රදේශයකට යයි. මෙම තාක්ෂණයට සැලකිය යුතු බලශක්ති අවශ්යතා ද ඇති අතර එය ඇලුමිනියම් වෙළඳපොළ මිල ගණන් වලට ද බලපායි.
2. දෙවන පියවර: උණුසුම් රෝලිං
ඇලුමිනියම් ස්ලැබ් එකක් තුනී කිරීම සඳහා උණුසුම් රෝලිං කිරීම බොහෝ විට භාවිතා කරන ක්රමයකි. උණුසුම් රෝලිං කිරීමේදී, ලෝහය නැවත ස්ඵටිකීකරණයේ ස්ථානයට ඉහළින් රත් කර එය විකෘති කර තවදුරටත් හැඩගස්වනු ලැබේ. ඉන්පසු, මෙම ලෝහ තොගය රෝල් යුගල එකක් හෝ කිහිපයක් හරහා ගමන් කරයි. මෙය සිදු කරනුයේ ඝණකම අඩු කිරීමට, ඝණකම ඒකාකාර කිරීමට සහ අපේක්ෂිත යාන්ත්රික ගුණාත්මක භාවයක් ලබා ගැනීමට ය. ෆැරන්හයිට් අංශක 1700 ක උෂ්ණත්වයකදී පත්රය සැකසීමෙන් ඇලුමිනියම් දඟරයක් නිර්මාණය වේ.
මෙම ක්රමය මඟින් ලෝහ පරිමාව නියතව තබා ගනිමින් සුදුසු ජ්යාමිතික පරාමිතීන් සහ ද්රව්ය ලක්ෂණ සහිත හැඩතල නිපදවිය හැක. තහඩු සහ තහඩු වැනි අර්ධ නිමි සහ නිමි භාණ්ඩ නිෂ්පාදනය කිරීමේදී මෙම මෙහෙයුම් ඉතා වැදගත් වේ. කෙසේ වෙතත්, නිමි රෝල් කරන ලද නිෂ්පාදන සීතල රෝල් කරන ලද දඟරවලට වඩා වෙනස් වන අතර, ඒවා මතුපිට ඇති කුඩා සුන්බුන් නිසා අඩු ඒකාකාර ඝණකම ඇති බැවින් ඒවා පහත විස්තර කෙරේ.
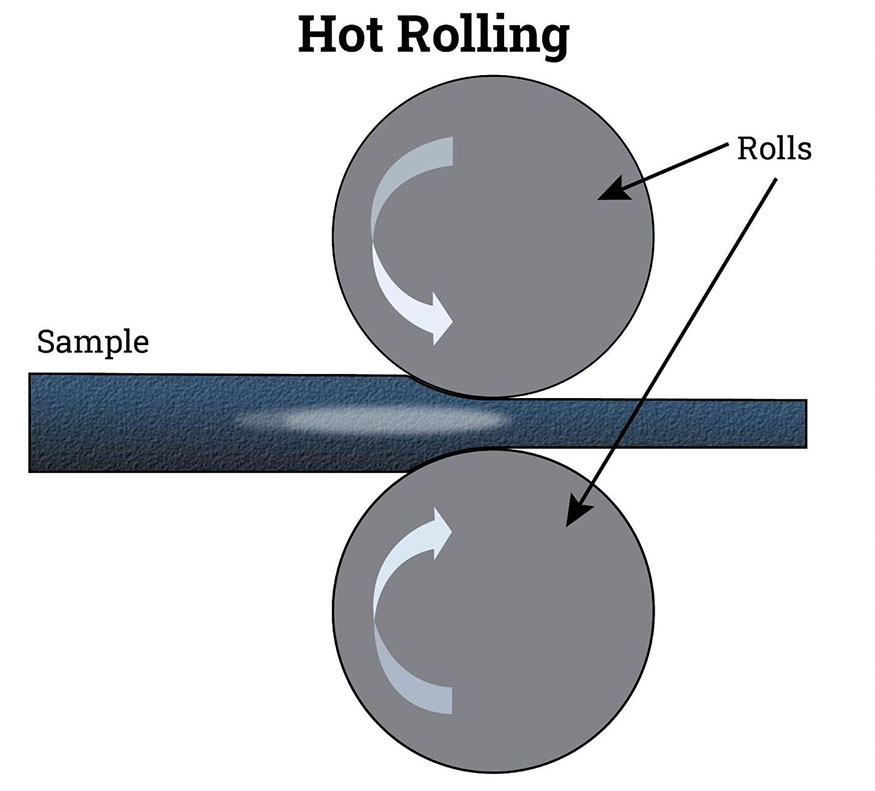
3. තුන්වන පියවර: සීතල රෝලිං
ලෝහ තීරු සීතලෙන් රෝල් කිරීම ලෝහ වැඩ කිරීමේ අංශයේ අද්විතීය ක්ෂේත්රයකි. "සීතල රෝල් කිරීමේ" ක්රියාවලියට ඇලුමිනියම් එහි නැවත ස්ඵටිකීකරණ උෂ්ණත්වයට වඩා අඩු උෂ්ණත්වයකදී රෝලර් හරහා දැමීම ඇතුළත් වේ. ලෝහය මිරිකා සම්පීඩනය කිරීමෙන් එහි අස්වැන්න ශක්තිය සහ දෘඪතාව වැඩි වේ. වැඩ-දැඩි කිරීමේ උෂ්ණත්වයේදී (ද්රව්යයක නැවත ස්ඵටිකීකරණ උෂ්ණත්වයට වඩා අඩු උෂ්ණත්වය) සීතල රෝල් කිරීම සිදු වන අතර වැඩ දැඩි කිරීමේ උෂ්ණත්වයට වඩා ඉහළින් උණුසුම් රෝල් කිරීම සිදු වේ - මෙය උණුසුම් රෝලිං සහ සීතල රෝලිං අතර වෙනසයි.
බොහෝ කර්මාන්ත සීතල රෝලිං ලෙස හඳුන්වන ලෝහ පිරියම් කිරීමේ ක්රියා පටිපාටිය භාවිතා කරමින් අපේක්ෂිත අවසාන මානය සහිත තීරු සහ තහඩු ලෝහ නිෂ්පාදනය කරයි. ඇලුමිනියම් වඩාත් ක්රියා කළ හැකි වන පරිදි රෝල් නිතර රත් කරනු ලබන අතර, ඇලුමිනියම් තීරුව රෝල් වලට ඇලී සිටීම වැළැක්වීම සඳහා ලිහිසි තෙල් භාවිතා කරයි. ක්රියාකාරී සියුම්-සුසර කිරීම සඳහා, රෝල් වල චලනය සහ තාපය වෙනස් කළ හැකිය. දැනටමත් උණුසුම් රෝල් කිරීමකට භාජනය වී ඇති ඇලුමිනියම් තීරුවක් සහ පිරිසිදු කිරීම සහ ප්රතිකාර කිරීම ඇතුළු අනෙකුත් ක්රියා පටිපාටි, ඇලුමිනියම් කර්මාන්තයේ සීතල මෝල් රෝලිං රේඛාවකට දැමීමට පෙර කාමර උෂ්ණත්වයට සිසිල් කරනු ලැබේ. ඇලුමිනියම් ඩිටර්ජන්ට් සමඟ සේදීමෙන් පිරිසිදු කර ඇති අතර මෙම ප්රතිකාරය ඇලුමිනියම් දඟරය සීතල රෝල් කිරීමට ඔරොත්තු දීමට තරම් දැඩි කරයි.
මෙම සූදානම් කිරීමේ පියවරයන් ආමන්ත්රණය කිරීමෙන් පසු, තීරු රෝලර් හරහා නැවත නැවතත් ගමන් කරන අතර, ක්රමයෙන් ඝණකම අඩු වේ. ක්රියාවලිය පුරාම ලෝහයේ දැලිස් තල කඩාකප්පල් වී විසන්ධි වන අතර එමඟින් වඩාත් දැඩි, ශක්තිමත් අවසාන නිෂ්පාදනයක් ලැබේ. ඇලුමිනියම් දැඩි කිරීම සඳහා සීතල රෝලිං වඩාත් ජනප්රිය ක්රම අතර වේ, මන්ද එය ඇලුමිනියම් තලා රෝලර් හරහා තල්ලු කරන විට එහි ඝණකම අඩු කරයි. සීතල රෝලිං තාක්ෂණයක් මඟින් ඇලුමිනියම් දඟරයක ඝණකම 0.15 mm දක්වා අඩු කළ හැකිය.
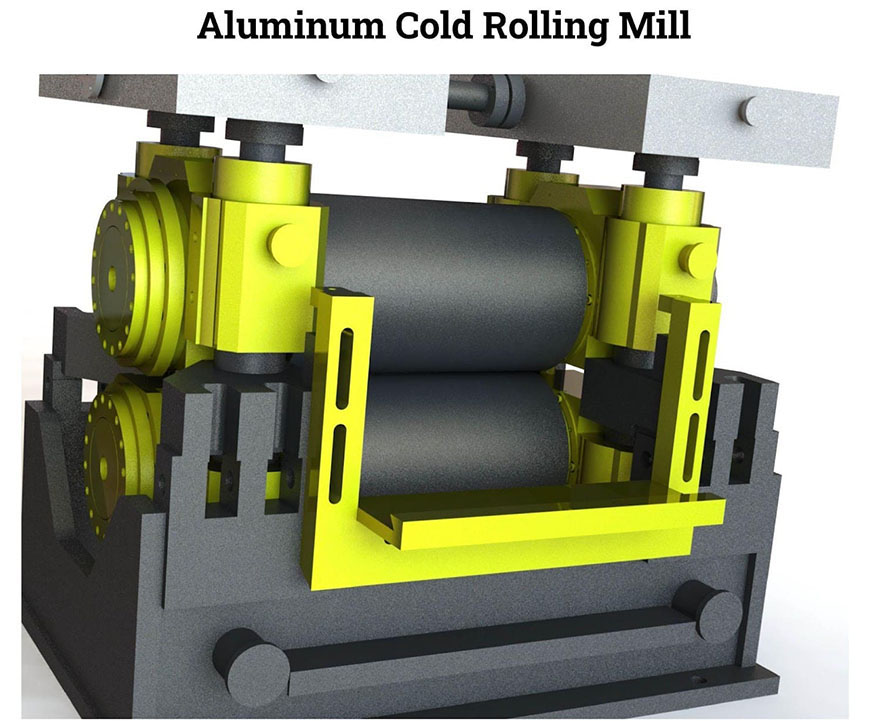
4. හතරවන පියවර: ඇනීලිං
ඇනීලිං ක්රියාවලියක් යනු ද්රව්යයක් වඩාත් නම්යශීලී සහ අඩු දෘඩ බවට පත් කිරීම සඳහා ප්රධාන වශයෙන් භාවිතා කරන තාප පිරියම් කිරීමකි. ඇනීලිං කරන ලද ද්රව්යයේ ස්ඵටික ව්යුහයේ විස්ථාපන අඩුවීම දෘඪතාව සහ නම්යතාවයේ මෙම මාරුවට හේතු වේ. බිඳෙනසුලු අසාර්ථකත්වය වළක්වා ගැනීමට හෝ පහත සඳහන් මෙහෙයුම් සඳහා ද්රව්යයක් වඩාත් ක්රියාකාරී කිරීමට, ද්රව්යයක් දැඩි කිරීමේ හෝ සීතල වැඩ කිරීමේ ක්රියා පටිපාටියකට භාජනය වූ පසු ඇනීලිං බොහෝ විට සිදු කරනු ලැබේ.
ස්ඵටිකරූපී ධාන්ය ව්යුහය ඵලදායී ලෙස නැවත සැකසීමෙන්, ඇනීල් කිරීම ස්ලිප් තල යථා තත්ත්වයට පත් කරන අතර අධික බලයකින් තොරව කොටස තවදුරටත් හැඩගැස්වීමට හැකියාව ලබා දෙයි. වැඩ-දැඩි කරන ලද ඇලුමිනියම් මිශ්ර ලෝහයක් මිනිත්තු තිහක සිට පැය තුනක් දක්වා වූ කලින් තීරණය කළ කාලයක් සඳහා 570°F සහ 770°F අතර නිශ්චිත උෂ්ණත්වයකට රත් කළ යුතුය. ඇනීල් කරන ලද කොටසෙහි ප්රමාණය සහ එය සෑදී ඇති මිශ්ර ලෝහය පිළිවෙලින් උෂ්ණත්වය සහ කාල අවශ්යතා තීරණය කරයි.
ඇනීලිං කිරීම මඟින් කොටසක මානයන් ස්ථාවර කරයි, අභ්යන්තර වික්රියා නිසා ඇතිවන ගැටළු ඉවත් කරයි, සහ සීතල ව්යාජකරණය හෝ වාත්තු කිරීම වැනි ක්රියා පටිපාටි අතරතුර ඇතිවිය හැකි අභ්යන්තර ආතතීන් අඩු කරයි. මීට අමතරව, තාප පිරියම් කළ නොහැකි ඇලුමිනියම් මිශ්ර ලෝහ ද සාර්ථකව ඇනීල් කළ හැකිය. එබැවින්, එය බොහෝ විට වාත්තු, නිස්සාරණය කරන ලද හෝ ව්යාජ ඇලුමිනියම් කොටස් සඳහා යොදනු ලැබේ.
ද්රව්යයක් සෑදීමේ හැකියාව ඇනීල් කිරීම මගින් වැඩි දියුණු වේ. අස්ථි බිඳීමක් ඇති නොකර දැඩි, බිඳෙන සුළු ද්රව්ය එබීම හෝ නැමීම අභියෝගාත්මක විය හැකිය. ඇනීල් කිරීම මෙම අවදානම ඉවත් කිරීමට උපකාරී වේ. ඊට අමතරව, ඇනීල් කිරීම යන්ත්රෝපකරණ හැකියාව වැඩි කළ හැකිය. ද්රව්යයක අධික බිඳෙනසුලු බව නිසා අධික මෙවලම් ඇඳීමට හේතු විය හැක. ඇනීල් කිරීම මගින් ද්රව්යයක දෘඪතාව අඩු කළ හැකි අතර එමඟින් මෙවලම් ඇඳීම අඩු කළ හැකිය. ඉතිරිව ඇති ඕනෑම ආතති ඇනීල් කිරීම මගින් ඉවත් කරනු ලැබේ. හැකි සෑම තැනකම අවශේෂ ආතතීන් අඩු කිරීම සාමාන්යයෙන් හොඳම වේ, මන්ද ඒවා ඉරිතැලීම් සහ අනෙකුත් යාන්ත්රික ගැටළු වලට තුඩු දිය හැකිය.
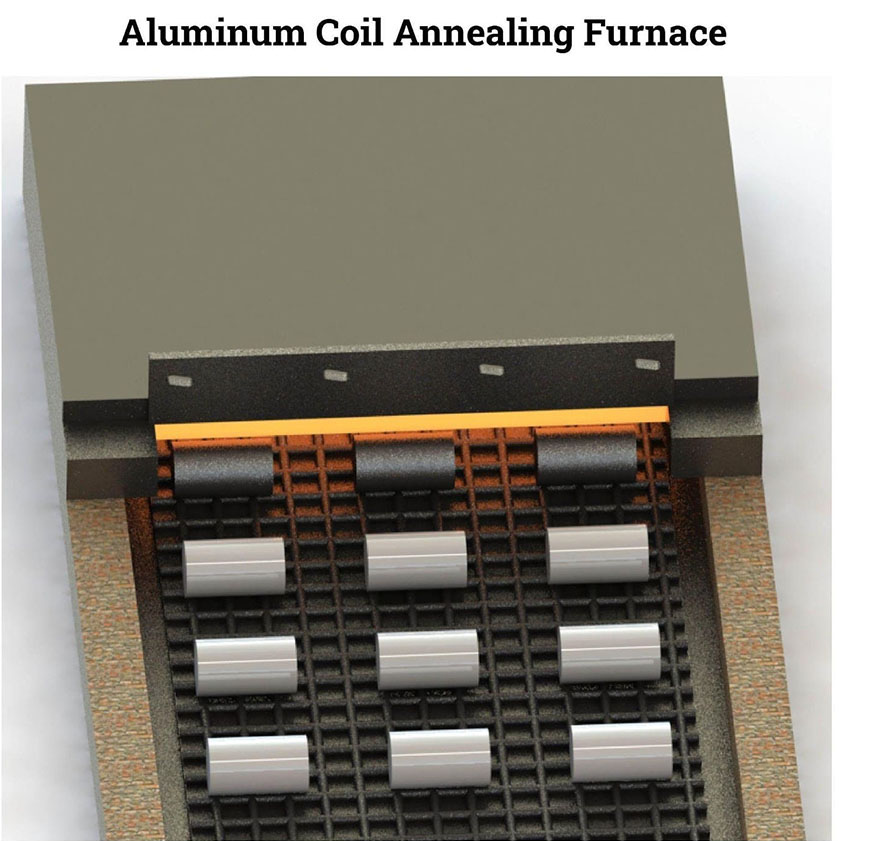
5. පස්වන පියවර: කැපීම සහ කැපීම
ඇලුමිනියම් දඟර ඉතා දිගු අඛණ්ඩ රෝලයකින් නිෂ්පාදනය කළ හැකිය. කෙසේ වෙතත්, දඟරය කුඩා රෝල් වලට ඇසුරුම් කිරීම සඳහා, ඒවා පෙති කපා ගත යුතුය. මෙම කාර්යය ඉටු කිරීම සඳහා, ඇලුමිනියම් රෝල් ස්ලිටින් උපකරණ හරහා ධාවනය කරනු ලබන අතර එහිදී ඇදහිය නොහැකි තරම් තියුණු තල නිවැරදි කැපුම් සිදු කරයි. මෙම මෙහෙයුම සිදු කිරීමට විශාල බලයක් අවශ්ය වේ. යොදන බලය ඇලුමිනියම්වල ආතන්ය ශක්තිය ඉක්මවා යන විට ස්ලිටර් රෝලය කුඩා කැබලිවලට බෙදයි.
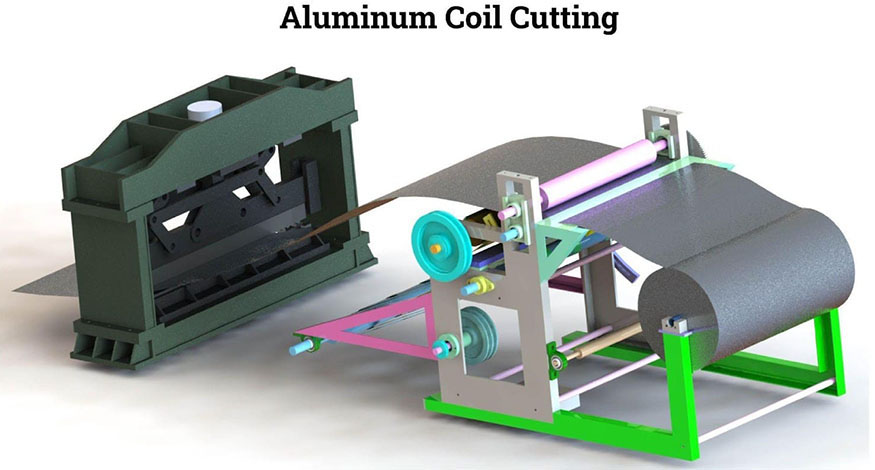
ස්ලිටිං ක්රියාවලිය ආරම්භ කිරීම සඳහා, ඇලුමිනියම් අන්කොයිලර් එකක තබා ඇත. පසුව, එය භ්රමණ පිහි කට්ටලයක් හරහා යවනු ලැබේ. අපේක්ෂිත පළල සහ නිෂ්කාශනය සැලකිල්ලට ගනිමින් හොඳම ස්ලිට් දාරය ලබා ගැනීම සඳහා තල ස්ථානගත කර ඇත. ස්ලිට් ද්රව්ය ප්රතිකොයිලර් වෙත යොමු කිරීම සඳහා, ද්රව්යය පසුව බෙදුම්කරුවන් හරහා පෝෂණය වේ. ඉන්පසු ඇලුමිනියම් මිටි කර නැව්ගත කිරීම සඳහා සූදානම් කිරීම සඳහා දඟරයකට ඔතා ඇත.
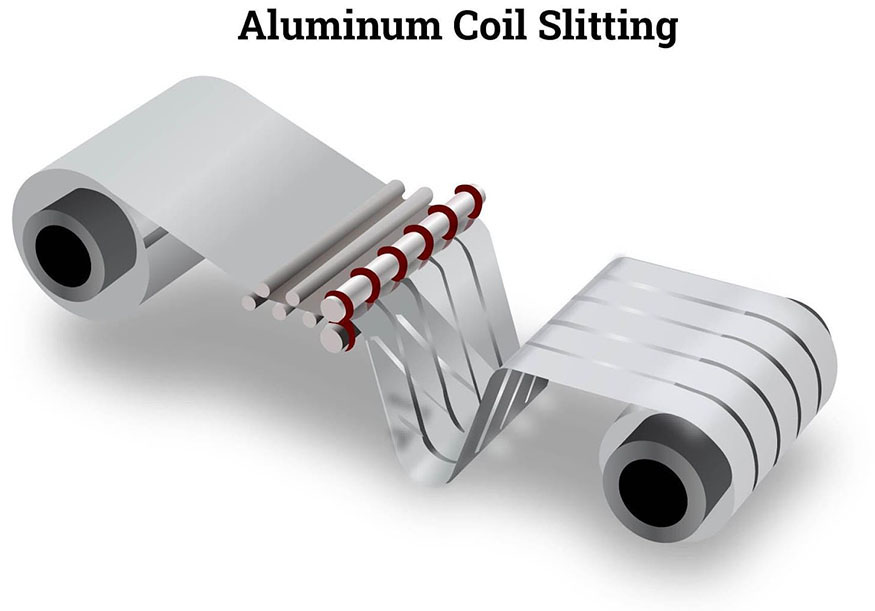
ජින්දලායි වානේ සමූහය ප්රමුඛ ඇලුමිනියම් සමාගමක් වන අතර ඇලුමිනියම් දඟර/තහඩු/තහඩු/තීරු/නල/තීරු සැපයුම්කරු වේ. අපට පිලිපීනය, තානේ, මෙක්සිකෝව, තුර්කිය, පකිස්ථානය, ඕමානය, ඊශ්රායලය, ඊජිප්තුව, අරාබි, වියට්නාමය, මියන්මාරය, ඉන්දියාව ආදී රටවලින් ගනුදෙනුකරුවන් සිටී. ඔබගේ විමසීම් එවන්න, වෘත්තීයමය වශයෙන් ඔබට උපදෙස් දීමට අපි සතුටු වන්නෙමු.
ක්ෂණික ඇමතුම් අංකය:+86 18864971774වෙචට්: +86 18864971774වට්ස්ඇප්:https://wa.me/8618864971774
විද්යුත් තැපෑල:jindalaisteel@gmail.com sales@jindalaisteelgroup.com වෙබ් අඩවිය:www.jindalaisteel.com/ වෙබ් අඩවිය
පළ කිරීමේ කාලය: දෙසැම්බර්-19-2022